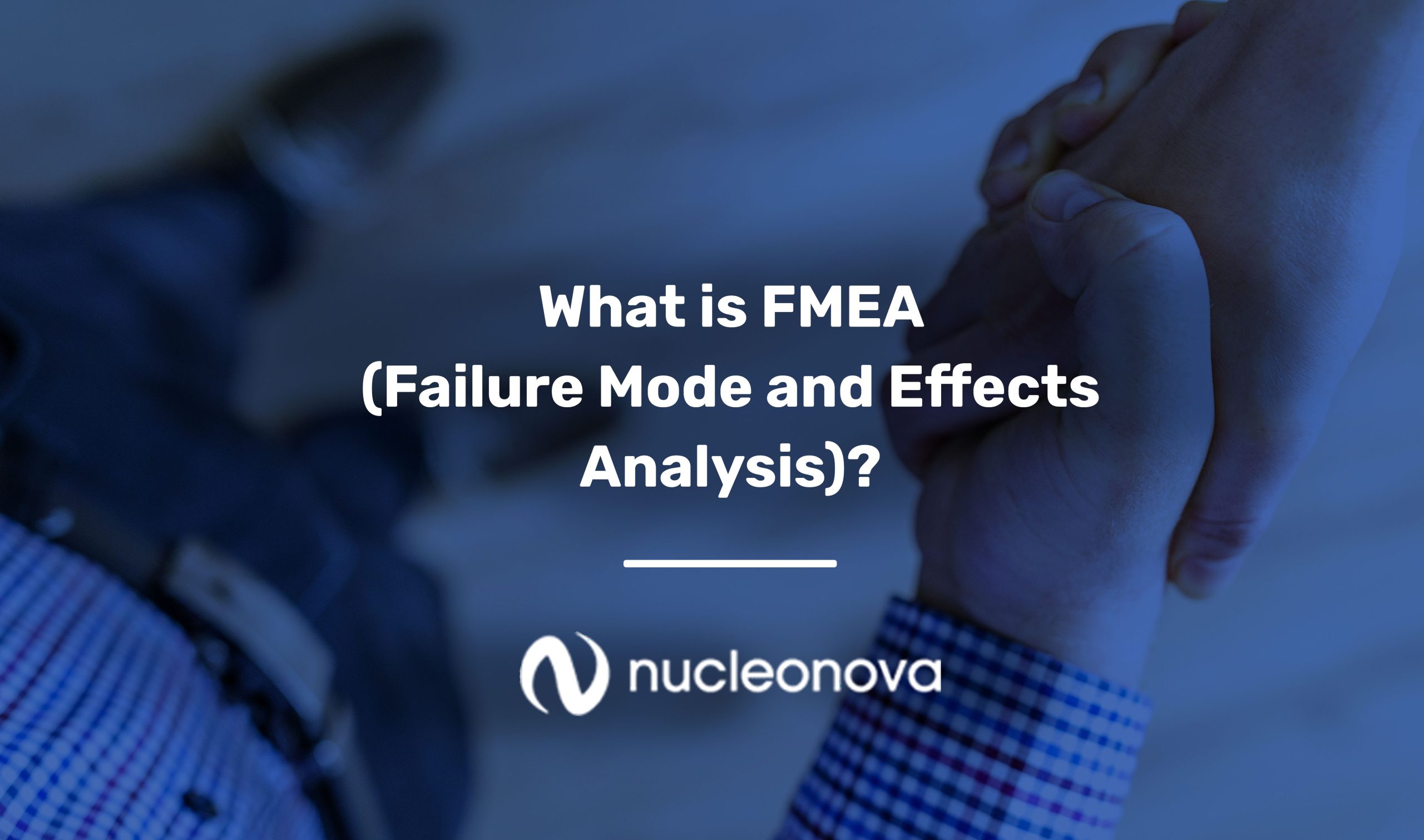
30 Jan What is FMEA (Failure Mode and Effects Analysis)?
FMEA is an effective methodology that helps us to predict the ways in which a design or process can fail and analyze its consequent effects. It is very useful in the design of a new product or service or to examine the impact of changes to an existing process/product.
What is Failure Mode and Effects Analysis?
Failure Mode and Effects Analysis (FMEA) is a structured methodology for identifying potential errors in a design or manufacturing process of a product or service, in order to establish and apply the necessary corrections.
FMEA is an effective tool to evaluate the reliability of a product/system and to quantify and reduce the risk associated with each potential failure point detected.
It is a method that complements good engineering practice, because:
- It analyzes failure modes, i.e., it analyzes the different ways in which a product or process can present a problem that affects its performance or efficiency. For example, a design error in software or a deficiency in raw materials.
- It analyzes the effects, i.e., it analyzes the consequences or problems that each failure mode can generate. For example, cost overruns of a product, waste within a process or damage to a customer.
Category or types of FMEA
On a large scale, the FMEA method can be of two types:
Design FMEA
Design FMEA, or Design Failure Mode and Effects Analysis DFMEA, examines the likelihood that a product will perform poorly, have a reduced service life, or have safety issues, due to:
– Design geometries.
– Material properties.
– Tolerance ranges.
– The effect of an environment.
– Interaction with other systems or components, etc.
DFMEA can be used to evaluate a new design, an existing design to which modifications are applied, or an existing design that needs to change cycle or working environment.
Process FMEA
Process FMEA, or Process Failure Mode and Effects Analysis PFMEA, allows the evaluation of each process step in order to identify failures and potential hazards that can cause reliability degradation, safety problems, environmental hazards, etc. Normally, these deficiencies have their origin in:
– Human errors.
– Errors in methodology.
– Problems in machinery or materials.
– Measurement errors, among other causes.
Steps for the development of an FMEA
A Failure Mode and Effects Analysis must be designed with specific details, according to the standards of the company or industry that will apply it. But in a general way, an FMEA procedure involves the following steps:
INITIAL STAGE:
-
- Form a multidisciplinary team, with specialized professionals with experience in the product/service design process, manufacturing, quality control, maintenance, sales, customer service, marketing, etc.
- Establish the objectives and scope of the FMEA. In detail and using flow charts.
- Identify the product.
- Detail the operation of the product, its uses and its components. Identify the failures (possible and real). This is done based on information gathering and the experience of the team members.
- Design a block diagram, which allows visualizing the components, their functions and interrelationships.
ANALYSIS STAGE:
-
- Elaborate the FMEA matrix for each component and function.
- Include each function, each failure mode and its corresponding effect. The severity of each effect should be considered.
- Analyze the effects derived from each failure mode.
- Determine the level of risk. Calculating the priority risk number of each error, based on the severity (S), the probability of occurrence (O) and the evidence or criteria for detection (D) of the error.
- Define the consequences or effects of each deficiency.
- Establish the corrective measures and prevention controls to be implemented.
POST-ANALYSIS STAGE: Corrective actions must be implemented.
CONTINUOUS OPTIMIZATION: The FMEA analysis should be performed periodically for quality improvement.
What are the benefits of using the FMEA matrix?
Applying the FMEA methodology facilitates the early detection of failures in the design or manufacturing process of a product, which in turn offers the following benefits for industries:
– Reduce costs and development times of products, services or processes.
– Prevent unplanned process downtime, which avoids associated costs and loss of performance.
– Avoid product malfunction, which also avoids dissatisfied customers and consequent complaints.
– Improve existing products, increasing their competitiveness against other products.
– Detect various options to reduce risks.
– Verify and validate design or process changes.
When to perform FMEA?
Failure Mode and Effects Analysis is mainly performed in the following cases:
– In the design of a new process or product.
– To make changes in an existing process.
– To increase the quality of a process or product.
– To understand the failures or problems in a process.
In addition, let us remember that the reliability and quality of a product, a service or an operational process must be continuously examined and optimized. Therefore, it is very useful to perform FMEA periodically.
Some applications of FMEA
Failure Mode and Effects Analysis is one of the most widely used methods to mitigate risk and increase process reliability. It is widely used in the aerospace, automotive, electrical and computer industries.
Among the applications of FMEA are the analysis of:
– Systems and software, evaluating each of their functionalities and detecting errors in their designs.
– Equipment and machinery, in order to increase their quality.
– Product design, before developing the prototype or starting production.
– Manufacturing and assembly processes.
– The service processes and each of their phases, before starting them up and making them available to the customer.
Nuclonova, engineering, procurement and quality
At Nucleonova we have a team of qualified engineers and technicians with extensive experience to accompany you and offer you an answer in each of the phases of the project.
We carry out an integral management, from the conceptual design and detailed engineering to the coordination and supervision of the works. We prepare the necessary documentation and technical studies in evaluations such as process improvement or Failure Mode and Effects Analysis (FMEA).
In Nucleonova we help you to analyze and promote the development of your project, process or product. If you need more information, contact us, we will deliver the solution you need.